Nằm trong khu Công nghiệp Đại Đồng – Hoàn Sơn, Tỉnh Bắc Ninh, phía bắc Thành Phố Hà Nội, Việt Nam. Công ty VSTT được thành lập từ năm 2011, đến nay công ty có 2 nhà xưởng với diện tích 3,200 m2 và tổng số CBCNV là hơn 100 người.
Công ty đang tham gia sản xuất và cung cấp những linh kiện cho ngành công nghiệp phụ trợ như: Các chi tiết hàn, dập và gia công từ kim loại cho thị trường Xe máy – Ô tô và sản phẩm công nghiệp khác.
Năm 2024, công ty Sigma VSTT được chọn là 1 trong 5 nhà cung cấp được Toyota Việt Nam hỗ trợ cải tiến sản xuất theo chương trình hợp tác với Cục Công nghiệp, Bộ Công Thương.
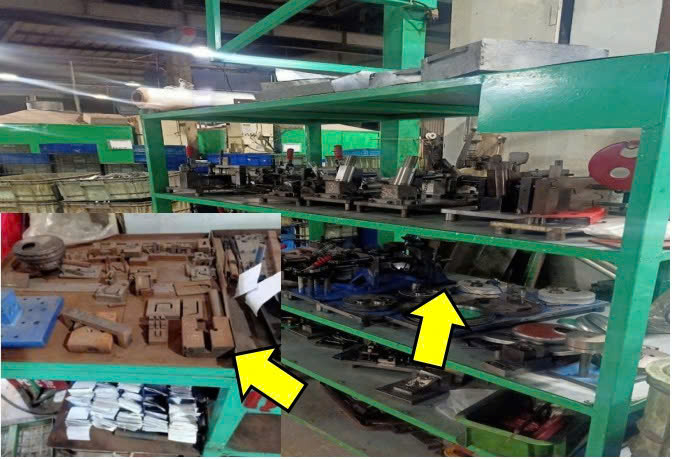
Theo ban lãnh đạo công ty, hiện trạng của công ty là hệ thống sản xuất chưa hoàn thiện, còn nhiều lãng phí. Ví dụ, hàng hóa, vật liệu tồn kho nhiều, không phân định khu vực rõ ràng, cách quản lý kho theo hình thức nhập trước xuất trước FIFO vẫn chưa áp dụng nên lãng phí nguyên vật liệu. Kỹ sư, công nhân làm việc phải thao tác mất nhiều thời gian, mất an toàn.
Theo tư vấn của Toyota Việt Nam, công ty Sigma đã áp dụng hàng loạt hoạt động cải tiến 5S, Kaizen. Đơn cử như về hoạt động cải tiến 5S điển hình, việc làm giá để khuôn đã được thay đổi. Từ chỗ nguyên vật liệu để trên giá lộn xộn, không có nhãn mác thì nay, tình trạng này chấm dứt. Trên giá loại bỏ các vật dụng không cần thiết, việc phân loại Jig được kiểm theo mã và theo khách hàng. Nhờ đó, công nhân có thể tìm lấy Jig dễ hơn. Dòng chảy sản xuất chưa tối ưu, không thuận chiều, đi rích rắc. Công ty gặp tình trạng tồn kho cả những sản phẩm dở dang. Khi sắp xếp lại layout hợp lý hơn, thu hẹp được khoảng cách dây chuyền hàn, quãng đường di chuyển giảm tới 245m và diện tích giảm tới 200m2.
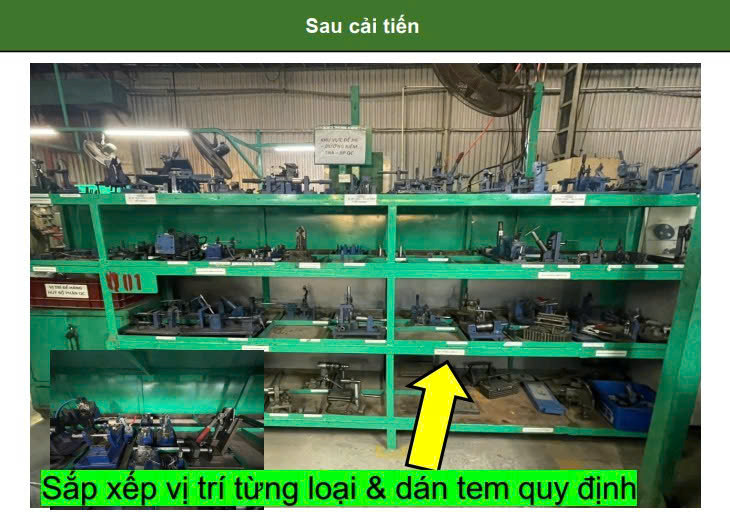
Đáng chú ý, trong hoạt động Kaizen, công ty đã thiết kế lại cơ cấu chuyển linh kiện dập. Trước đây, công nhân lấy linh kiện phải thao tác nhiều, mất thời gian thì nay, khi sử dụng chuyển động lên xuống của máy dập để đưa hàng ra thùng đựng, bộ phận này giảm đi 1 nhân sự, năng suất tăng 12%.
Vấn đề an toàn lao động cũng được chú trọng. Trước đây, người đi vào nhà máy tự do đi vào khu vực làm việc của máy móc thiết bị khá tự do nhưng sau khi được tư vấn, công ty đã bổ sung rào chắn, đảm bảo an toàn và dễ quản lý 5S.
Đối với cân bằng dây chuyền hàng, công ty giảm được 2 người/ca, góp phần tăng năng suất lên tới 14%. Đáng chú ý, sau khi layout nhà máy được sắp xếp lại, diện tích tồn kho đã giảm tới 30%.
Sau khi cải tiến sản xuất, công ty giảm tới 6 nhân sự, tương đương giảm 792 triệu đồng/năm; tăng hiệu suất lao động lên 12% tương đương 95 triệu đồng/năm. Thời gian tồn kho giảm từ 18 ngày xuống còn 12 ngày, giúp tiết kiệm chi phí tới 145 triệu đồng/tháng. Riêng diện tích sản xuất giảm tới 200m2. Với giá thuê trung bình 133 USD/năm, công ty đã giảm tới 665 triệu đồng/năm tiền thuê mặt bằng.
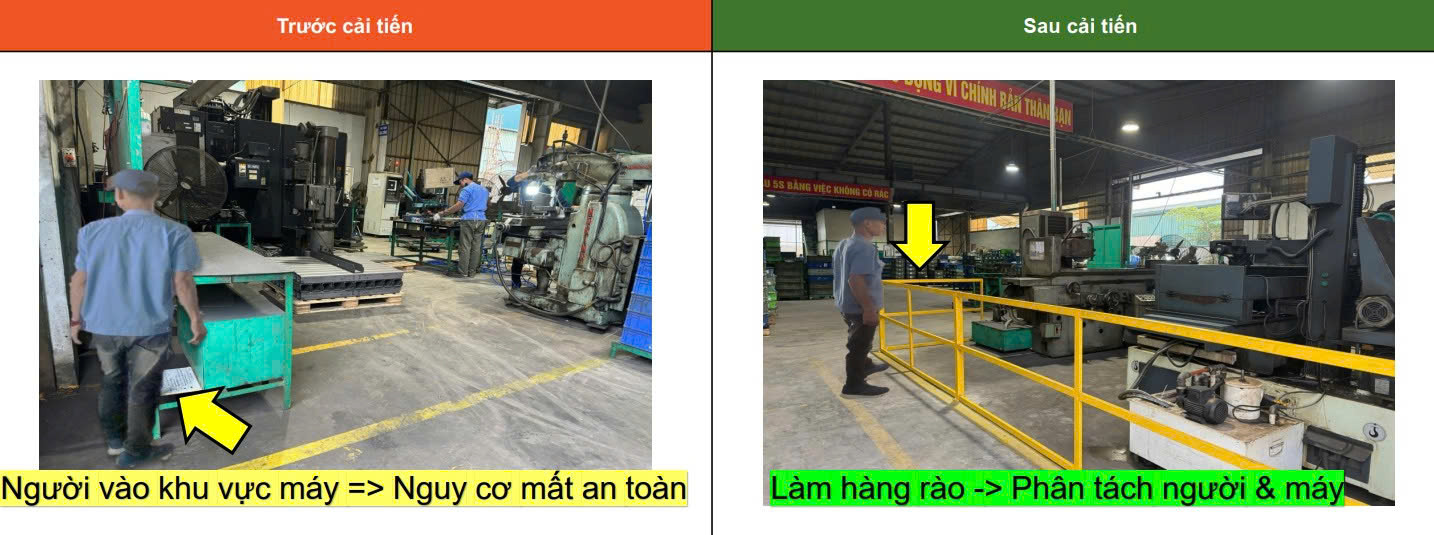
Tổng hợp kết quả thực hiện phương pháp Kaizen theo tư vấn của Toyota Việt Nam, Sigma tiết kiệm được tới 1,697 tỷ/năm. Tiếp tục thực hiện cải tiến sản xuất, ước tính đến quý I năm 2025, công ty sẽ tiết kiệm được 2,45 tỷ đồng/năm. Tiến tới bước ba, khi hoàn thiện toàn bộ hoạt động cải tiến, công ty có thể tiết kiệm tới 3,1 tỷ đồng/năm.
Ông Nguyễn Thái Bình, Trưởng khối điều hành công ty Sigma chia sẻ, đây là lần đầu tiên công ty được tiếp cận phương pháp sản xuất mới và cảm thấy chương trình hỗ trợ của Cục Công nghiệp và Toyota rất có ý nghĩa đối với doanh nghiệp. “Chúng tôi mong muốn được đào tạo chuyên sâu hơn hoặc có các cơ hội học hỏi trong các hoạt động cải tiến, đặc biệt làm TPS motion nhằm tăng năng suất lao động và giảm tải sức cho người lao động”, ông Bình nhấn mạnh.
Băng Dương